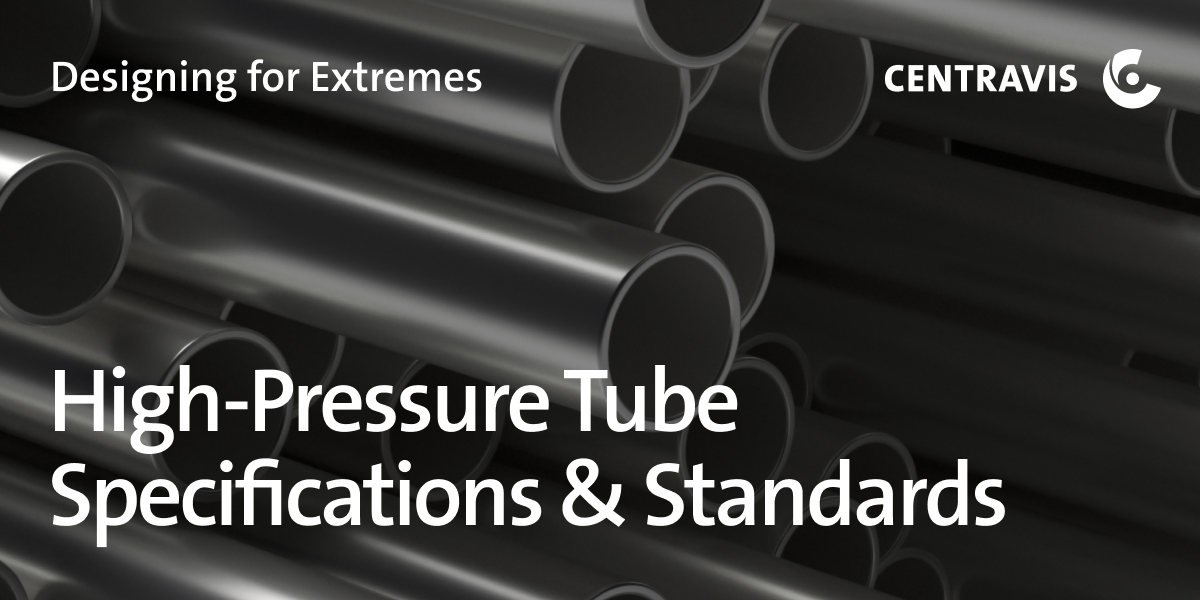
In critical industries such as energy, aerospace, petrochemical, and nuclear, high-pressure applications require materials that can withstand extreme conditions while maintaining structural integrity. Seamless stainless steel tubes are often the material of choice due to their superior mechanical properties, resistance to corrosion, and ability to operate efficiently under high-pressure environments.
This article will explore the essential specifications and standards that define the design of high-pressure tubes, including material selection, mechanical properties, testing methods, and the regulatory framework governing their production and application.
Understanding High-Pressure Tube Requirements
High-pressure tubes are integral to systems where fluid or gas is transported under elevated pressure, such as in pressure vessels, hydraulic systems, or steam lines. These tubes must maintain performance under extreme pressure, temperature fluctuations, and potential corrosive environments. The primary challenges in designing high-pressure tubes include ensuring:
- Mechanical Strength: High resistance to tensile and compressive forces is essential to prevent deformation or failure under load.
- Corrosion Resistance: Tubes must resist the degradation caused by environmental factors such as acids, bases, and high-temperature media.
- Fatigue Resistance: In systems subject to repeated loading and unloading cycles, resistance to fatigue and crack propagation is crucial.
- Durability: The tube must maintain its integrity over the lifetime of the equipment, which often includes exposure to harsh conditions such as high temperatures, pressure cycling, and aggressive chemicals.
Key Material Specifications for High-Pressure Tubes
Austenitic Stainless Steel
Austenitic stainless steel grades such as 304L and 316L are widely used in high-pressure applications. These materials offer excellent resistance to general corrosion, pitting, and crevice corrosion, making them ideal for industries like chemical processing, oil & gas, and power generation. They also offer good mechanical strength and are relatively easy to weld, which is a critical factor in complex assemblies.
Duplex and Super Duplex Stainless Steel
Duplex stainless steels and super duplex grades combine the strength of ferritic steels with the corrosion resistance of austenitic steels. These materials are especially suited for high-pressure applications in aggressive environments, where there is a high risk of chloride stress corrosion cracking and pitting. Duplex and super duplex steels provide higher strength than austenitic grades while maintaining excellent resistance to corrosion, making them ideal for offshore and subsea applications, as well as chemical processing under high pressures.
Nickel Alloys
In extremely corrosive or high-temperature environments, nickel-based alloys, such as Inconel, are used due to their outstanding performance under both high-pressure and high-temperature conditions. Nickel alloys provide exceptional resistance to corrosion, oxidation, and thermal fatigue, which is why they are often used in critical industries like aerospace, power generation, and petrochemical.
Particular attention should be given to Balev 304L® and Balev 316L® from Centravis — these grades are specifically designed for use in high-pressure conditions. They offer a unique combination of strength, corrosion resistance, and ductility. In terms of mechanical properties, they can even surpass some duplex steel grades, demonstrating enhanced reliability and operational durability. With the ability to use thinner-walled tubes without compromising safety, Balev 304L® and Balev 316L® also provide economic benefits and reduce the weight of structures, contributing to more environmentally responsible projects.
Key Mechanical Properties for High-Pressure Tubes
High-pressure tubes must meet specific mechanical requirements to ensure their functionality in extreme environments. These properties are generally defined by industry standards and specifications, including:
- Yield Strength: The ability of a tube to withstand stress without permanent deformation is a key factor. High yield strength ensures that the tube can handle high-pressure loads without failing.
- Tensile Strength: This is the maximum stress a tube can withstand before breaking. It is critical in preventing catastrophic failures under extreme conditions.
- Elongation: Elongation indicates the ductility of the material, which is important for absorbing stress without fracturing. High elongation is particularly important in applications that involve dynamic loading or bending.
- Hardness: Hardness tests can provide insight into the tube’s resistance to abrasion and surface wear, which are important in high-pressure applications exposed to abrasive particles.
Testing Methods and Standards for High-Pressure Tubes
High-pressure tubes must undergo rigorous testing to ensure their performance in the field. These tests verify that the tubes meet the required mechanical properties, can withstand the intended pressures, and are free from defects. Common testing methods include:
- Hydrostatic Testing: This is the most common test for high-pressure tubes. The tube is filled with water, and pressure is applied to check for leaks or deformation. This test simulates the internal pressure conditions the tube will face in operation.
- Tensile Testing: Tensile tests are performed to measure the strength and ductility of the material. The tube is pulled until it fails, and the results help determine its ability to handle high-pressure stress.
- Impact Testing: This test is used to assess the toughness of the tube, particularly at low temperatures, where materials may become brittle.
- Nondestructive Testing (NDT): Methods such as ultrasonic testing (UT), eddy current testing, and radiographic testing are used to detect internal defects, such as cracks, inclusions, or porosity, that could compromise the tube’s integrity under pressure.
Industry Standards for High-Pressure Tubes
High-pressure tubes must conform to various international standards that define the material properties, testing requirements, and dimensions of the tubes. Some of the key standards include:
ASTM Standards
The American Society for Testing and Materials (ASTM) sets forth a number of standards for high-pressure tubes, including:
- ASTM A312: Standard Specification for Seamless and Welded Austenitic Stainless Steel Pipes.
- ASTM A269: Standard Specification for Seamless and Welded Stainless Steel Tubing for General Service.
- ASTM A789: Standard Specification for Seamless and Welded Ferritic/Austenitic Stainless Steel Tubing for General Service.
These standards define the chemical composition, mechanical properties, dimensions, and testing methods that ensure the tubes can perform safely in high-pressure environments.
ASME Standards
The American Society of Mechanical Engineers (ASME) also plays a crucial role in setting standards for high-pressure tubes, particularly for use in boilers and pressure vessels. ASME Boiler and Pressure Vessel Code (BPVC) provides guidelines for material selection, design, and construction of pressure vessels that operate at high pressures.
ISO Standards
International Organization for Standardization (ISO) has established standards for materials used in high-pressure applications, including:
- ISO 1127: Stainless Steel Tubes for the Food, Pharmaceutical, and Chemical Industries.
- ISO 3183: Petroleum and Natural Gas Industries — Steel Pipes for Pipeline Transportation Systems.
These international standards ensure consistency and reliability of tubes used in critical applications across different regions and industries.
Applications of High-Pressure Tubes
High-pressure tubes are widely used in critical industries such as:
- Energy Sector: In power plants, high-pressure tubes are essential for steam lines, heat exchangers, and boilers. These tubes must endure high temperatures and pressures, often in corrosive environments.
- Petrochemical Industry: High-pressure tubes are used in refining, chemical processing, and gas transportation. They must handle extreme pressure conditions and exposure to aggressive chemicals.
- Aerospace Industry: Tubes in aerospace applications must withstand high pressures and extreme temperatures. They are used in systems such as hydraulic circuits and fuel lines.
- Nuclear Industry: Tubes used in nuclear reactors must be able to handle high pressure, temperature, and radiation. The materials must maintain structural integrity over extended periods of time.
Conclusion
Designing high-pressure tubes for extreme conditions is a complex process that requires careful material selection, adherence to stringent mechanical properties, and conformance to industry standards. Whether it’s for energy, aerospace, petrochemical, or nuclear applications, seamless stainless steel tubes offer the best combination of strength, corrosion resistance, and durability for high-pressure environments. By understanding the key specifications and standards for high-pressure tubes, engineers can ensure the reliability and safety of critical systems, contributing to more efficient operations and longer service life.
As industries continue to push the limits of pressure and temperature in their operations, the role of high-quality high-pressure tubes will become even more crucial in ensuring safety, performance, and longevity in the most demanding applications.