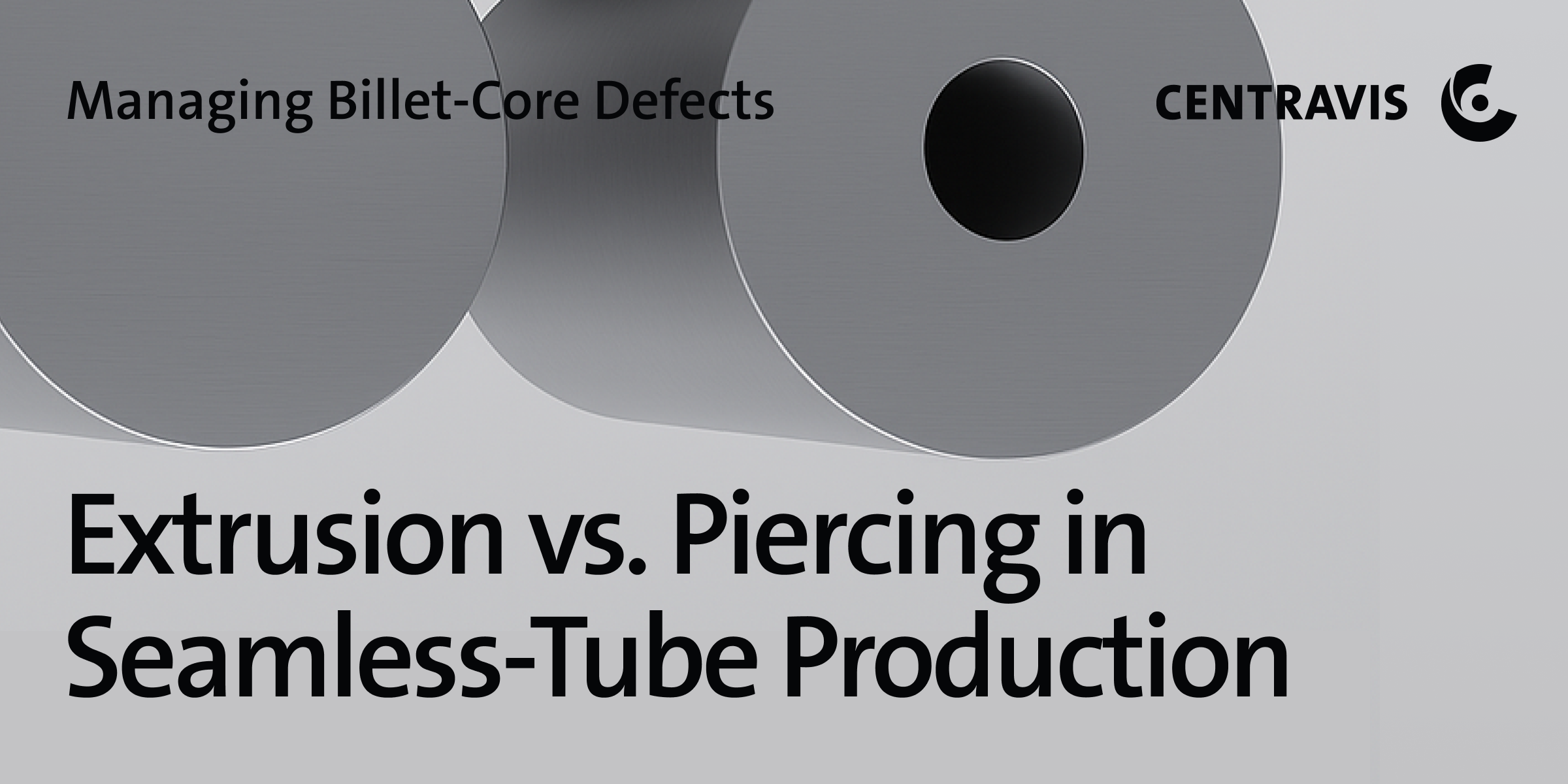
In stainless-steel tube manufacturing, internal soundness is dictated less by the finishing pass and more by what happens deep inside the starting billet. Non-metallic inclusions, micro-shrinkage cavities, and chemical segregation concentrate along the centreline of any cast product. How a hot-working route—piercing or forward hot extrusion—deals with that flawed core largely determines the service life of the finished tube. The discussion below maps each step from billet preparation to final quality control, allowing engineers to match process capability with project requirements.
The Nature of Core Defects
During solidification, grains grow from the mould wall inward; the centre is the last zone to freeze and therefore the natural collector of impurities. Oxide and sulfide particles, unable to fit into the solidifying lattice, are pushed ahead of the solidification front and trapped in the core. Simultaneously, volumetric contraction creates micro-shrinkage voids, while elements such as carbon, phosphorus, or molybdenum segregate, forming bands of altered chemistry.
Left unaddressed, these defects propagate as stringers or pores along the inner diameter (ID) of a tube, acting as crack embryos under cyclic pressure, undermining pitting resistance in chloride media, and accelerating high-temperature creep damage.
Billet Preparation for Piercing
Piercing relies on reheating a solid billet to ~1150 °C in gas-fired rotary furnaces. Extended soak times generate thick scale and promote surface carburisation. Once plastic, the billet is gripped by skewed rolls that both rotate and feed it toward a stationary mandrel. Shear stresses split the hot core, and the original centre metal flows radially outward, becoming part of the ID surface.
Because the central zone remains intact until it fractures, any inclusions or segregated bands are smeared along the new bore. Typical fallout includes intrawall porosity, mid-wall laminations, or axial hairline cracks—defects that demand intensive nondestructive testing (phased-array UT, eddy current) and, when detected, costly grinding or rejection.
Billet Preparation for Extrusion
Forward hot extrusion adopts a preventive strategy. Prior to heating, the billet undergoes deep-hole drilling that removes roughly 10-16 % of its diameter, physically extracting the defect-laden core. The hollow billet is then induction-heated in 8-12 minutes, rapid heating minimises scale, while a powdered-glass coating melts into a low-friction film that both lubricates and shields the surface.
During the four- to eight-second extrusion stroke, the billet is compressed through a die under hydrostatic pressure. This action collapses residual microporosity, eliminates shear-type tearing, and realigns grains into a fine, uniform flow—attributes prized for duplex, super-duplex, and Ni-base alloys where phase balance and corrosion performance hinge on tight thermal control.
Comparative Perspective
From an ID-cleanliness standpoint, extrusion is inherently superior because the core—where most discontinuities reside—is removed before hot work begins. The resulting tubes exhibit lower inclusion counts and smoother bores, often allowing reduced inspection sampling. Piercing equipment, however, is less capital-intensive and offers high throughput for commodity austenitic grades.
However, even in seemingly low-spec applications, hidden inclusions introduced during piercing can later surface during machining or forming—potentially leading to costly part rejection or rework. As a result, extrusion may prove economically justified even for standard or mid-range products, especially in precision-critical operations.
Project economics therefore pivot on two questions:
- Can the service environment tolerate occasional ID inclusions or laminations? If yes, piercing may deliver acceptable quality at lower cost.
- Is zero-defect integrity mandatory—whether we are talking about nuclear primary-loop tubing, hydrogen refuelling lines, high-purity urea synthesis coils, ultra-high-pressure hydraulic circuits for mobile equipment, safety-critical automotive fuel/exhaust assemblies, or any machined component where a single inclusion can scrap an entire part? In these and many similar situations, extrusion’s premium—typically 15-25 % on finished-tube price—quickly pays back through longer inspection intervals, higher fatigue life, less machining fallout, and lower warranty exposure.
- Lead-time considerations also matter. Extrusion can supply single lengths up to 24 m, eliminating circumferential welds in heat-exchanger or reformer coils, whereas piercing mills seldom exceed 12 m without subsequent welding.
Practical Selection Guidelines
- Define ID acceptance criteria—maximum inclusion size, Ra, and permissible lamination rate—within the RFQ.
- Audit billet macrostructure by macro-etch or UT mapping; heavily segregated heats favour extrusion.
- Match alloy family to process. Duplexes, super-duplexes, and Ni-base grades benefit from extrusion’s shorter thermal exposure and lower friction, reducing sigma-phase formation and surface scuffing.
- Consider length and bending needs. Where long, weld-free coils or tight bending radii are essential, extrusion provides concentric walls and finer grain, translating into predictable forming behaviour.
Conclusion
When core-born defects threaten reliability, success hinges on selecting the hot-working route that neutralises those flaws—not merely masks them. Piercing delivers cost efficiency and adequate quality for non-critical services, yet it leaves inclusions and micro-shrinkage to migrate onto the ID, demanding heavier inspection and tighter process windows. Hot extrusion, by contrast, physically removes the billet core, applies uniform compressive loading, and produces a fine-grained, inclusion-lean tube wall. The result is lower scatter in mechanical properties, longer corrosion life, and higher confidence under cyclic or high-pressure duty. For projects where unplanned shutdowns, warranty claims, or safety margins carry real economic weight—nuclear heat exchangers, hydrogen or urea lines, super-critical steam coils—the premium on extrusion is quickly repaid. In short, when zero-defect integrity is the specification rather than the aspiration, extrusion is not just an option; it is the process of choice.