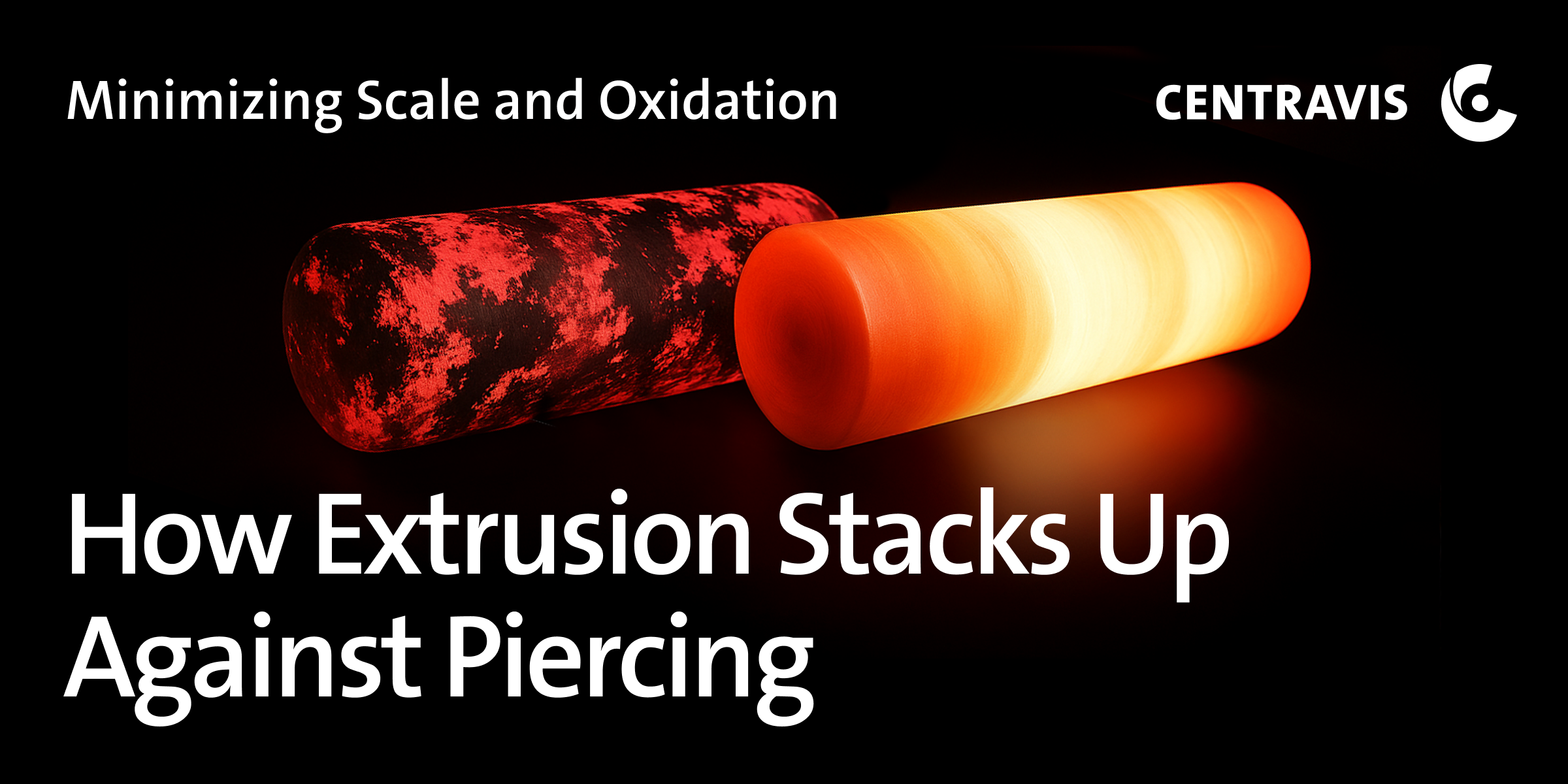
Oxide scale is the sworn enemy of stainless-steel tube performance. Once an adherent scale layer forms on a hot billet or tube shell, several downstream problems follow in its wake: chromium depletion at the steel surface, pitting initiation sites after pickling, embedded scale particles that trigger crevice corrosion, and extra grinding or acid consumption to restore a clean finish. For heat-exchanger coils, instrumentation capillaries, or catalytic-reformer tubes, those microscopic defects translate into real-world leaks or premature replacements.
Because scale forms mainly during billet heating, any hot-working route that limits exposure time or shields the surface enjoys a sizeable quality advantage. That is where the comparison between piercing and hot extrusion becomes pivotal.
How Scale Forms—And Why It Matters
Stainless steel resists corrosion in service because a thin, self-healing Cr₂O₃ film covers the surface. When we heat a billet to 1 150 – 1 250 °C in an oxidising atmosphere, the growth kinetics shift. A thick, multi-layered scale of iron‐, chromium- and manganese-rich oxides develops in minutes. Oxygen penetrates grain boundaries, chromium is drawn out of the austenite matrix, and micro-voids emerge beneath the scale. After deformation, these voids can turn into linear pitting or “spider-web” intergranular attack.
For a tube intended to carry high-chloride media or superheated steam, any residual scale pocket becomes the corrosion cell that shortens its life.
Heating Profiles: Piercing vs. Extrusion
Piercing mills need billets thoroughly soaked through because the centre must reach the ductility required for fracturing and plug expansion. Typical cycle:
- Gas-fired rotary furnace
- Residence time 45–60 min (Ø 200 mm billet)
- Furnace atmosphere ≈ 21 % O₂ + combustion products
Scaling rates climb exponentially after the first 15 min; by 45 min the surface scale can be 0.25 – 0.35 mm per side. Operators descaler-spray the billet just before piercing, but oxide islands often remain, especially in surface depressions. As the billet elongates around the plug, those islands smear into longitudinal laps on the ID and OD.
Extrusion, in contrast, pre-drills the billet, coats ID/OD with a borosilicate-based glass, and uses induction or short tunnel furnaces:
- Induction heating coil or compact walking-beam
- Heat-up 8 – 12 min (same diameter)
- The billet is heated first, and only after reaching forming temperature is it coated with molten glass, where it serves to reduce friction and protect the surface from oxidation.
- Surface protected by molten glass film (μ ≈ 0.08)
The glass both reduces friction and acts as an oxygen barrier; actual oxide growth is typically < 0.05 mm, most of which stays within the glass and flakes off after extrusion. Because useful temperature is retained, the billet can be extruded in ~ 4 s, leaving little time for secondary scale.
When Piercing Still Fits
Piercing remains the workhorse for large volumes of boiler, OCTG and line-pipe grades where surface Ra targets are moderate and downstream scarfing or honing is acceptable. For 300-series stainless with heavy walls (> 8 mm) and less stringent ID cleanliness, cost per tonne is lower, and scale removal becomes a manageable post-process step.
Conclusion
Scale and oxidation are not merely aesthetic concerns—they dictate corrosion life, weldability, and mechanical consistency. Because extrusion minimises furnace residence time and shields the billet with a glass lubricant, it starts the tube’s life with a cleaner, chromium-rich skin. Whether the end-use involves ultra-hygienic instrumentation lines, duplex or austenitic heat-exchanger coils, thin- and medium-wall condenser tubes for chloride environments, precision hydraulic circuits, safety-critical automotive fuel and exhaust components, or even machine-shop blanks where hidden inclusions drive up re-work costs, this surface advantage proves decisive across a wide production spectrum. Piercing retains its seat for mass-market dimensions, yet when maximum surface integrity and corrosion margin are non-negotiable, extrusion simply stacks up stronger.