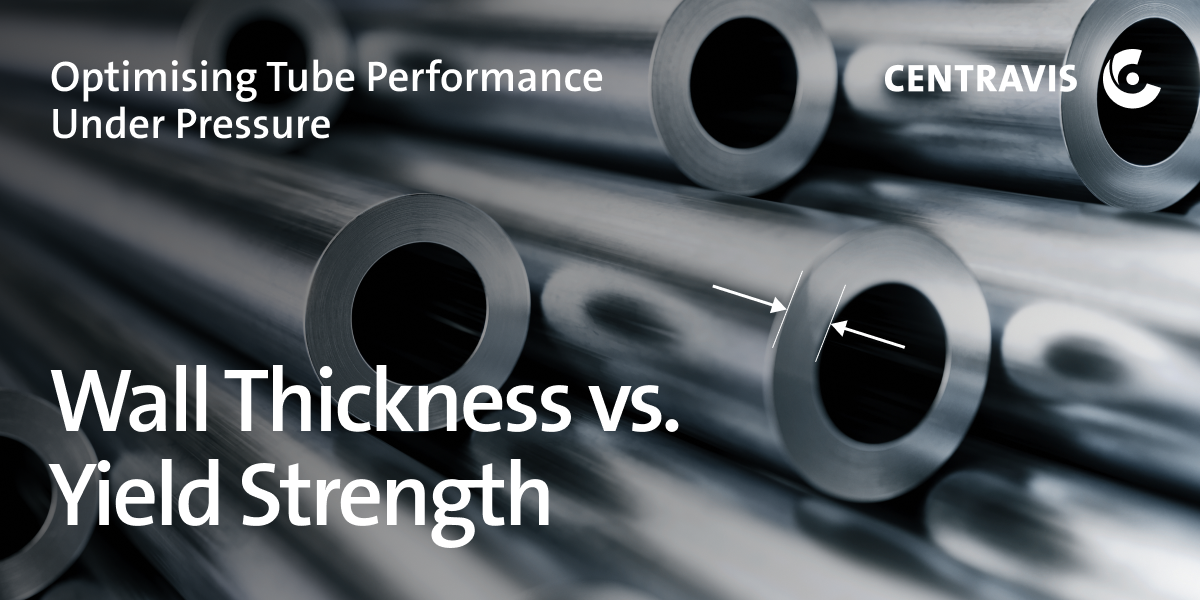
In critical industries, the performance of tubes under pressure is an essential consideration in the design and operation of systems that involve high-pressure environments. From power generation and oil & gas pipelines to aerospace and chemical processing, tubes are subjected to extreme forces, and their performance under pressure is paramount. A key factor in determining tube performance is the relationship between wall thickness and yield strength — two critical attributes that influence how a tube behaves under stress.
In this article, we will explore how wall thickness and yield strength interact to impact tube performance, and how engineers can optimise these factors to ensure tubes function safely and efficiently under pressure. Drawing from industry best practices and expert insights from Centravis, a leading supplier of seamless stainless steel tubes, we will discuss the practical applications of these concepts and the role of material selection in tube performance.
The Importance of Wall Thickness in Tube Design
The wall thickness of a tube plays a crucial role in determining its pressure-bearing capacity. In simple terms, the thicker the wall, the higher the pressure the tube can withstand without yielding. Wall thickness directly influences the tube’s internal pressure capacity, as it determines the amount of material that resists deformation and prevents the collapse of the tube under stress.
For applications involving high pressures, such as in the oil and gas sector, power plants, and chemical reactors, the wall thickness must be designed to resist not only the internal pressure but also other external forces, including mechanical loads, vibrations, and temperature fluctuations. Thick-walled tubes are essential in preventing deformation, rupture, or failure in critical systems. However, increasing the wall thickness is not always the best solution, as it can introduce trade-offs related to material cost, weight, and processability.
Yield Strength: The Material’s Ability to Resist Deformation
Yield strength is another critical property of tube materials, and it defines the maximum stress a material can withstand without undergoing permanent deformation. It is an essential factor when considering how a tube will perform under pressure, as it determines how much force can be applied to the tube before it begins to yield or deform irreversibly.
For high-pressure applications, materials with higher yield strength are preferred because they can handle more stress without deforming. In practical terms, a tube with higher yield strength can endure greater internal pressure without losing its shape, which is essential for ensuring the structural integrity of the system.
Stainless steel, particularly grades such as Balev 304L® and Balev 316L® from Centravis, and advanced alloys like duplex stainless steels, offers excellent yield strength, making it an ideal material for high-pressure applications. By selecting the appropriate material with optimal yield strength, engineers can ensure that the tube will not deform under pressure, even with thinner walls.
The Trade-Off: Wall Thickness vs. Yield Strength
While increasing the wall thickness of a tube improves its pressure-bearing capacity, it also increases its weight and cost. A thicker tube requires more material, which in turn results in higher production costs and may impact the overall weight of the system. This can be especially problematic in industries like aerospace, where every kilogram counts, and weight reduction is a critical design consideration.
On the other hand, materials with higher yield strength allow for thinner walls without compromising the tube’s ability to withstand high pressure. By choosing a material with superior yield strength, it is possible to reduce the wall thickness while still maintaining performance under pressure. This is a crucial factor in optimising tube design, as it offers a balance between strength, weight, and cost.
For example, Centravis’s Balev 304L® and Balev 316L® are designed specifically for high-pressure applications. These materials not only offer excellent yield strength but also provide corrosion resistance and ductility, enabling the use of thinner-walled tubes without compromising safety. This material optimisation results in cost savings and weight reduction, making it an ideal solution for industries that require high-performance tubes.
Optimising Tube Performance Under Pressure
To optimise tube performance under pressure, engineers must strike a balance between wall thickness, yield strength, and material selection. Achieving this balance involves careful consideration of the following factors:
Material Selection
Choosing the right material is crucial for optimising tube performance. Stainless steels, such as 304L, 316L, and duplex alloys, provide a balance of yield strength and corrosion resistance, making them suitable for high-pressure environments. Duplex stainless steels, for example, offer higher strength compared to austenitic steels, allowing for the use of thinner walls while maintaining excellent resistance to corrosion.
Stress Analysis
Engineers must conduct a detailed stress analysis to determine the maximum pressure the tube will experience in its intended application. This analysis helps identify the optimal wall thickness and material required to withstand these pressures without yielding. By performing this analysis, engineers can ensure that the tube’s design is efficient, cost-effective, and capable of performing under extreme conditions.
Performance Testing
Rigorous testing is essential to validate the tube’s ability to perform under pressure. Hydrostatic testing, tensile testing, and fatigue testing are commonly used to evaluate a tube’s performance. These tests simulate real-world conditions and provide valuable data on how the tube will behave under stress, allowing engineers to fine-tune the design to optimise performance and reliability.
Manufacturing Considerations
Manufacturing methods, such as extrusion and piercing, also play a significant role in tube performance. For example, extrusion allows for the creation of tubes with uniform wall thickness and improved mechanical properties, making it suitable for high-pressure applications. Piercing, on the other hand, may result in internal defects, such as porosity, which could compromise the tube’s strength under pressure.
Practical Applications and Case Studies
In industries such as oil and gas, power generation, and aerospace, the optimisation of tube performance under pressure is critical. For example, in offshore drilling operations, where high-pressure and corrosive environments are common, using tubes with a combination of high yield strength and optimal wall thickness is essential to prevent failures. In these applications, tubes like Centravis’s Balev 316L® can be used to ensure reliable performance while reducing the overall weight and cost of the system.
Similarly, in the aerospace sector, where lightweight materials are essential, engineers can optimise tube performance by selecting materials with high yield strength, allowing for the use of thinner walls without sacrificing performance. This not only reduces the weight of the aircraft but also contributes to fuel efficiency and overall operational costs.
Conclusion
Optimising tube performance under pressure requires a careful balance between wall thickness and yield strength. By selecting the right material with high yield strength and carefully considering the wall thickness, engineers can create tubes that are strong, lightweight, and cost-effective, ensuring reliable performance in high-pressure environments.
Through advanced materials like Balev 304L® and Balev 316L®, Centravis provides a practical solution for high-pressure applications, offering the perfect combination of strength, corrosion resistance, and ductility. With the right design and material selection, tubes can be optimised to perform safely and efficiently under extreme conditions, driving innovation and ensuring the success of critical industries.
In high-pressure applications, the key to success lies in understanding the interplay between wall thickness, yield strength, and material properties. By leveraging these insights, engineers can optimise tube design, reduce costs, and ensure long-term performance and reliability.