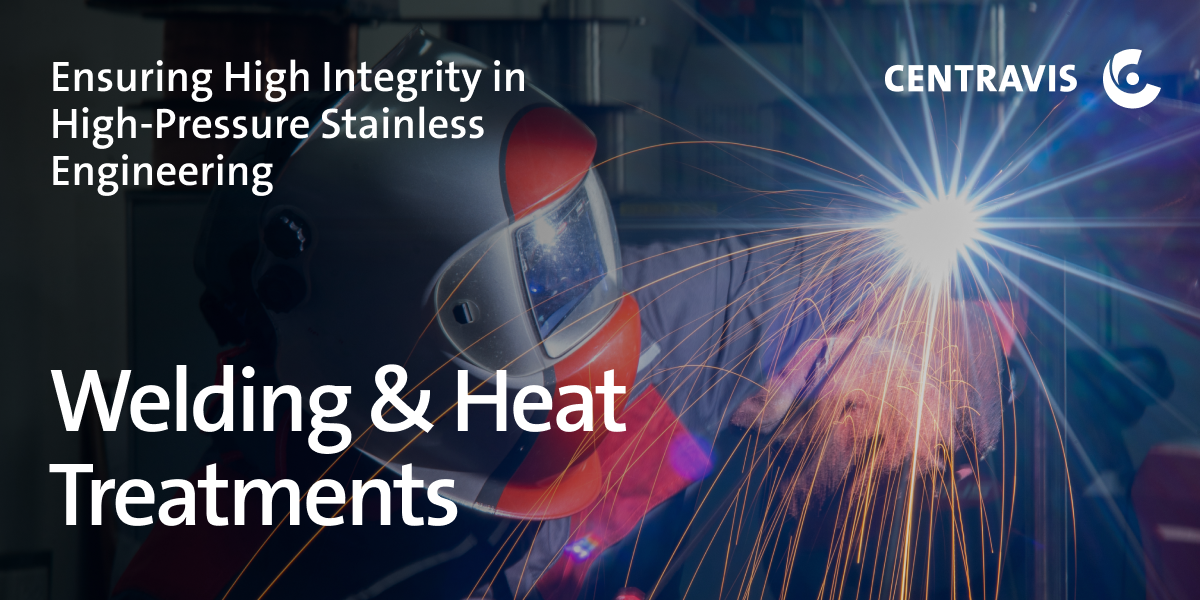
Seamless stainless steel pipes are widely used in critical infrastructure industries where they operate under high pressure. In energy, petrochemical, chemical processing, and aerospace industries, high-pressure pipes must withstand extreme operational conditions. To achieve high integrity of pipes, two main processes are critical: welding and heat treatment.
In this article, we will explore how welding and thermal processes affect the quality of seamless stainless steel pipes used under high pressure, and how these technologies help ensure high reliability and durability of pipes in critical industries.
The Importance of Welding in High-Pressure Engineering
Welding is one of the most important operations in the production of pipes used under high pressure. Weld seams must provide the same strength and leak-tightness as the base material of the pipe: this ensures that no defects or damage occur during operation.
Types of Welding
For welding high-pressure pipes, methods such as gas metal arc welding (MIG/MAG), tungsten inert gas (TIG) welding, and plasma welding are most commonly used. Each of these methods has its advantages depending on the requirements of the weld seam:
- TIG welding ensures high-quality weld seams, ideal for stainless steels, where minimal deformation and high seam strength are important.
- MIG/MAG welding allows for welding thicker materials and can be used in situations where high welding speed is required.
- Plasma welding is used for high-precision weld seams in special industries, particularly in aerospace and nuclear industries.
The Impact of Welding on Material Properties
The welding process creates a heat-affected zone (HAZ) where the material undergoes structural changes. This can negatively affect its strength and corrosion resistance. To ensure high integrity of the weld seam, it is important to choose the right welding technology and materials for electrodes and filler materials, as well as to apply special cooling methods and maintain control over the welding temperature.
Heat Treatment: Enhancing Mechanical Properties
Heat treatment is another crucial stage in the production of high-pressure pipes. It involves several processes aimed at improving the mechanical properties of the material — strength, ductility, corrosion resistance, and fatigue strength.
Types of Heat Treatment
For pipes operating under high pressure, two main heat treatment processes are particularly important:
- Annealing — a process in which the material is heated to high temperatures and then slowly cooled. This process helps reduce internal stresses, improve ductility, and reduce the risk of crack formation in pipes under high loads.
- Quenching and aging — processes that increase the hardness and strength of the material. These are especially important for duplex and super duplex steels that come into contact with aggressive substances such as oil, gas, or chemical compounds.
The Impact of Heat Treatment on Pipe Materials
Proper heat treatment ensures the optimal combination of strength, ductility, and corrosion resistance. These characteristics are critical for pipes working in high-pressure and aggressive environments. For example, steels that undergo heat treatment can have significantly improved corrosion resistance. Such materials are used for pipes in the petrochemical or marine industry, where pipes not only work under high pressure but also are exposed to aggressive chemical influences.
The Importance of Quality Control of Weld Seams and Heat Treatment
To ensure high integrity of pipes used under high pressure, stringent quality control must be conducted at every stage of production — from welding to heat treatment. Key testing methods include:
- Non-destructive testing (NDT). Methods such as ultrasonic testing (UT), eddy current testing, and radiography help detect defects in weld seams or material structure that could reduce pipe reliability.
- Strength and fatigue testing. Testing pipes for their ability to withstand high and cyclic loads is an important aspect of using pipes in high-pressure systems.
- Corrosion resistance testing. This method is particularly important for pipes working in aggressive environments such as seawater or chemical reagents.
Application of Welding and Heat Treatment in Various Industries
Welding and heat treatment technologies play an important role in various industries where seamless stainless steel pipes are used under high pressure:
- Energy: In thermal and nuclear power plants, high-pressure pipes must withstand high temperatures and pressures. Welding and heat treatment help ensure their reliability and durability.
- Oil and gas industry: A key characteristic of pipelines for transporting oil and gas is their ability to withstand high pressures and aggressive conditions. Welding and proper heat treatment ensure the long service life of pipes.
- Chemical and petrochemical industries: Under high temperatures and pressures, welding and heat treatment help achieve optimal mechanical properties and corrosion resistance of pipes.
- Aerospace industry: Here, the use of welding and thermal processes allows for the creation of strong, lightweight, and corrosion-resistant pipes for aviation and space systems.
Conclusion
Welding and heat treatment are key technologies that determine the quality and reliability of pipes used in high-pressure environments. Applying the correct welding methods and heat treatments allows for the manufacturing of pipes with high strength, corrosion resistance, and durability. This is especially important for the safety and efficiency of systems in various industrial sectors.
The right choice of material, welding methods, and proper heat treatment ensure the high integrity of pipes used under high pressure, extending their service life and reducing the risk of failure. Thanks to high-quality manufacturing, continuous quality control, and innovative technologies, Centravis guarantees products that meet the highest safety and reliability standards.